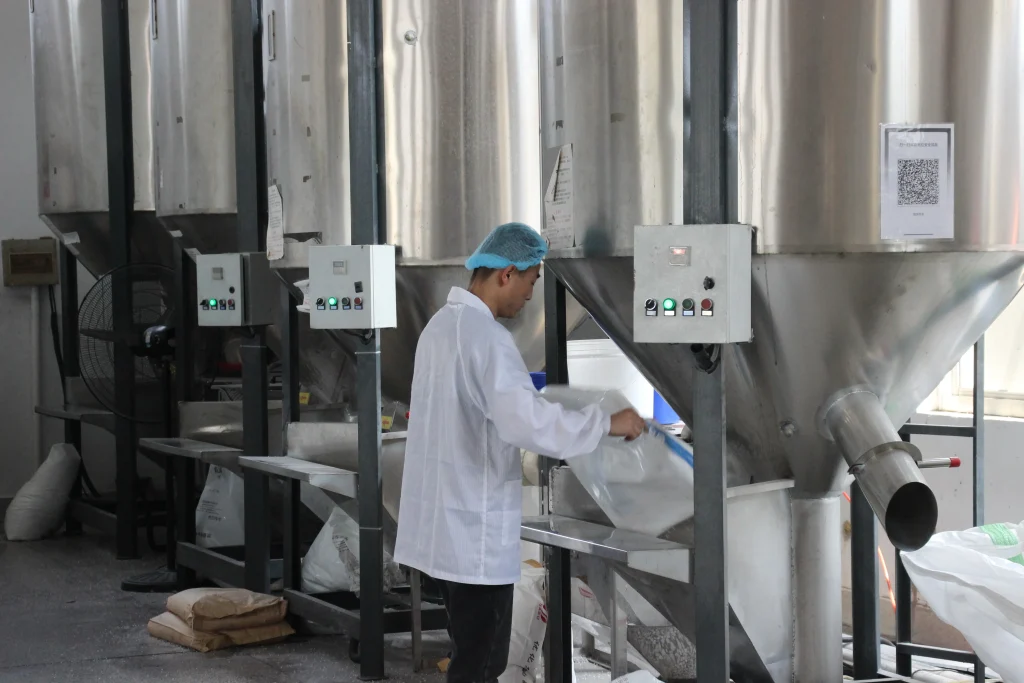
Electrical safety:
Plastic processing equipment is usually powered by electricity. When operating, ensure safe use of electricity and comply with relevant electrical regulations to avoid electric shock accidents.
Regularly check the integrity of wires, plugs and sockets to prevent aging, damage, leakage or short circuits that could lead to fires.
The equipment should have a good grounding system to ensure that the current can be quickly discharged in the event of a fault.
Thermal safety:
Injection molding, extrusion, blow molding and other processes all require heating to melt the plastic, so operators should pay attention to high temperature protection and stay away from heat sources to avoid burns.
Processing equipment must be operated in strict accordance with regulations during the heat treatment stage before and after work to prevent the risk of fire or explosion caused by overheating.
Use special tools to access hot parts, and regularly inspect and maintain heating elements and temperature control systems.
Fire prevention measures:
Corresponding fire prevention measures should be taken according to the characteristics of different plastic materials. For example, if PP plastic boards are not flame retardant, fireworks should be strictly prohibited during processing.
Equip fire-fighting equipment in the processing area to ensure that fires can be extinguished quickly in emergencies.
Machinery safety:
Operators should be familiar with the operating procedures and safety regulations of the equipment and should not clean, adjust or repair the equipment while it is in operation.
Safety doors, protective covers and other protective facilities of the equipment must not be dismantled or removed at will to ensure that personnel do not come into contact with moving parts.
Before starting up, conduct a comprehensive inspection of the equipment, including whether the bolts are tightened, well lubricated, and there are no abnormalities in the moving parts.
Personal protection:
Select appropriate personal protective equipment, such as anti-scald gloves, goggles, dust masks, etc., based on the hazards that may arise during the specific processing process.
For processing links that may produce toxic gases or dust, ventilation needs to be enhanced, and gas masks or other respiratory protection devices must be worn as needed.
Material management and environmental control:
Ensure the safety of storage and use of raw materials, especially flammable, explosive or toxic and harmful plastic raw materials must be properly kept.
Keep the working environment clean and tidy to reduce accidental injuries caused by littering, slippery floors and other factors.
Training and supervision:
All operators must receive strict safety training. Those who are not trained or fail the assessment are not allowed to work.
Establish and improve the safety production system, assign dedicated personnel to be responsible for the supervision and management of safety production, and promptly discover and eliminate safety hazards.